Przewody gotowe – profesjonalne wykonanie
Dysponujemy pełną paletą możliwości wykonywania przewodów gotowych. Oprócz klasycznych metod montażu mechanicznego końcówek dysponujemy specjalistycznymi prasami do końcówek zaciskanych oraz technologią spawania końcówek do węży metalowych. W zakresie technologii spawalniczych posiadamy odpowiednie uprawnienia i wykwalifikowany personel. Po montażu, przewody gotowe poddawane są rygorystycznej kontroli i próbom potwierdzającym ich jakość i spełnienie oczekiwanych parametrów.
Gotowe, sprawdzone przewody są trwale znakowane według naszych standardów lub zgodnie z życzeniem klienta.
Realizujemy też zamówienia na specjalne przewody gotowe wykonywane przez naszych dostawców. Są to węże z integralną wykładziną teflonową, węże metalowe i kompozytowe wielkogabarytowe, np. do przeładunków morskich, specjalistyczne węże gumowe z fabrycznie zawulkanizowanymi końcówkami.
Zobacz jak pracujemy
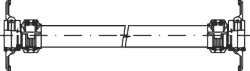
Co nazywamy przewodem elastycznym?
Pod pojęciem przewodów elastycznych rozumiemy węże elastyczne wyposażone w odpowiednie systemy złączne lub szybkozłączne. Najprostszym przykładem przewodu elastycznego jest wąż z dwoma końcówkami zamocowanymi za pomocą odpowiednich systemów np. obejm skorupowych lub opasek zaciskowych. Bardziej skomplikowane produkty zawierają szereg dodatkowych elementów niezbędnych do bezpiecznego użytkowania i spełnienia norm oraz dyrektyw np. przewód do przeładunku substancji niebezpiecznych, wyposażony w złącze zrywne, zawory odcinające itp.

Jak prawidłowo dobrać przewód?
Podstawowymi informacjami, niezbędnymi do dobrania przewodu są: średnica węża, długość przewodu, typ przyłączy, medium (rodzaj i temperatura), ciśnienie robocze, ewentualnie podciśnienie i środowisko pracy – czyli czynniki zewnętrzne, np. na zewnątrz, w hali itp. Nie znając tych parametrów nie możemy mówić o bezpiecznym i prawidłowym stosowaniu przewodów elastycznych. Aby ułatwić prawidłowe dobranie przewodu prosimy skorzystaj z naszego specjalnego konfiguratora przewodów, a nasi specjaliści będą w stanie szybko wyliczyć cenę. Prosimy o rozważne wypełnianie rubryk. Jeżeli nie są Państwo pewni posiadanych danych prosimy o ich sprawdzenie lub ewentualnie przyjąć odpowiedni margines bezpieczeństwa. Dla pełnego bezpieczeństwa zalecamy kontakt z naszymi przedstawicielami w celu wspólnego sprawdzenia czy wszystkie istotne czynniki zostały uwzględnione.
Określenie długości przewodu z końcówkami:
Długość przewodu bywa rozumiana w różny sposób, co może prowadzić do nieporozumień, zwłaszcza w przypadku końcówek z zagłębioną powierzchnią uszczelniającą. Prosimy zapoznać się z przykładowymi rysunkami definiującymi długość całkowitą Lc oraz długość części elastycznej Le przewodu oraz ich relacji do ogólnej długości przewodu L w przypadku zastosowania różnego typów końcówek i przy ich pomocy określić potrzebne Państwu szczegółowe wymiary. Plik PDF do pobrania
UWAGA!
Nie zaniżamy parametrów krytycznych takich jak ciśnienie, temperatura. Jeżeli w danym procesie występują rożne parametry zawsze podajemy najbardziej skrajne wartości. Najwyższe możliwe ciśnienie i największe podciśnienie. Najwyższą i najniższą temperaturę pracy. Jeżeli wysokość ciśnienia, temperatura pracy, rodzaj przewodzonej substancji itd. może powodować zagrożenie dla zdrowia lub życia ludzi zalecamy kontakt z naszym działem handlowym w celu sprawdzenia poprawności doboru.
Pamiętaj, jesteś odpowiedzialny za dokładność i poprawność podanych danych.
Konfigurator przewodów
Ze względu na ogromną ilość dostępnych wariantów i konfiguracji trudno zaprezentować w czytelny sposób wszelkie możliwe rozwiązania. Dla ułatwienia komunikacji z nami zamieszczamy poniżej konfigurator pozwalający sporządzić uproszczoną specyfikację potrzebnego przewodu i przesłać ją bezpośrednio do naszego działu handlowego. Nasi pracownicy niezwłocznie skontaktują się z Państwem, ustalą ewentualne dodatkowe potrzeby i przedstawią ofertę.
PRZEWODY GUMOWE
Elastyczność gumy w naturalny sposób sugerowała użycie tego materiału do budowy węży i tym samym kompletnych przewodów. Zastosowanie tej koncepcji w praktyce zaowocowało powstaniem całego szeregu rozwiązań, w którym głównym materiałem konstrukcyjnym węża są różne gatunki odpowiednio wzmocnionych elastomerów. Typowo, konstrukcja węża gumowego składa się z kilku warstw: warstwy wewnętrznej – dobranej odpowiednio do przepływającego przez wąż medium, warstwy wzmocnienia oraz warstwy zewnętrznej – pełniącej głównie funkcje ochronne dla węża.
Warstwa wewnętrzna
Zależnie od przeznaczenia węża (medium) wykonywana jest z jednej z wielu dostępnych mieszanek gumy, np. NR, NBR, EPDM, FKM, BR, itd. Głównym składnikiem mieszanki są wymienione z nazwy rodzaje elastomerów, natomiast zawierają one również inne substancje jak wypełniacze, barwniki, dodatki zapewniające własności antystatyczne itp. dające w efekcie pożądane właściwości. Z tego właśnie powodu nawet węże wykonane z tak samo określanego gatunku, a pochodzące od różnych producentów mogą się dość znacznie różnić się od siebie parametrami jak np. zakres temperatur pracy, jak i szczegółowymi właściwościami dotyczącymi poziomu odporności chemicznej, jakości antystatyki, odczuwalnej sztywności i zmiany tej sztywności wraz ze spadkiem temperatury, czy też przenikalności materiału dla przewodzonego medium. Oprócz cech wynikających z gatunku materiału znaczenie ma również technologia produkcji: ekstruzja daje materiał homogeniczny, podczas gdy nawijanie taśmy z gumy surowej na mandreli może skutkować niedoskonałym połączeniem pomiędzy poszczególnymi zwojami.
Ponieważ odporność mieszanek gumowych okazała się niewystarczająca dla niektórych rodzajów agresywnych substancji, od pewnego czasu poprawia się własności węży gumowych stosując wykładziny z zaawansowanych tworzyw sztucznych z grupy polietylenów i fluoropolimerów. Najczęściej obecnie spotykamy wykładziny z UPE, FEP i PTFE. Tego rodzaju węże posiadają bardzo dobrą odporność chemiczną i dość szeroki zakres zakresu temperatur, natomiast charakteryzują się podwyższoną sztywnością, zwłaszcza w niskich temperaturach. Istotne są także dodatkowe zalety tworzyw: bardzo wysoka odporność na ścieranie (w przypadku UPE), możliwość stosowania do substancji spożywczych. Jednakże – ze względu na możliwość uszkodzenia cienkiej warstwy wewnętrznej – wymagają stosowania dedykowanych końcówek pozbawionych głębokiego karbowania.
Nie do pominięcia jest także rosnąca rodzina węży produkowanych z gum termoplastycznych, a więc w odróżnieniu od elastomerów klasycznych nie wymagających procesu wulkanizacji. Jeśli chodzi o elastyczność to niejednokrotnie przewyższają one węże gumowe, wnosząc przy okazji atrakcyjne cechy swoich materiałów konstrukcyjnych: przejrzystość, wszechstronną odporność i czystość. Obecnie dostępne materiały to TPV i TPE
Wzmocnienie węża
Stosownie do przewidzianego rodzaju pracy: tłocznej lub ssawno-tłocznej uzyskuje się je odpowiednio kordem tekstylnym, oplotami z włókien lub drutu dla uzyskania wytrzymałości ciśnieniowej oraz spiralami ze stali lub twardego tworzywa – dla uzyskania wytrzymałości na podciśnienie.
Oprócz zrealizowania zaprojektowanej funkcji, tzn. osiągania zaprojektowanej wytrzymałości ciśnieniowej lub podciśnieniowej, technologia konkretnego rozwiązania mocno rzutuje na takie cechy węża jak jego ciężar, minimalny dopuszczalny promień zagięcia i odczuwalną elastyczność oraz podatność na zmianę objętości pod wpływem zmian ciśnienia. Trzeba pamiętać, że warstwa wewnętrzna węża gumowego musi być bardzo dobrze związana z pozostałymi warstwami – wewnętrzną i zewnętrzną w procesie wulkanizacji, co jest dość trudnym zadaniem ze względu na materiały z których wykonane jest wzmocnienie: włókna, druty i spirale z metalu lub tworzywa. Nie do pominięcia jest też fakt, że użyte materiały muszą posiadać wystarczającą odporność na substancje mogące migrować poprzez warstwę wewnętrzną do wnętrza węża.
Warstwa zewnętrzna
Ma za zadanie chronić wąż. Najbardziej oczywistymi czynnikami działającymi na wąż z zewnątrz jest tarcie na skutek manewrowania przewodem. Nie do pominięcia są także czynniki takie jak działanie promieniowania słonecznego, zmiennych warunków atmosferycznych. W konkretnych zastosowaniach dochodzą dodatkowe czynniki: substancje chemiczne, środowisko zanieczyszczone substancjami ropopochodnymi lub tłuszczami zwierzęcymi, wymaganie trudnopalności czy inne. Stosownie do tych zadań dobierane są odpowiednio mieszanki gumy, zazwyczaj nieco odmienne od tych stosowanych dla warstw wewnętrznych. Ostatnio dość często sięga się również do tworzyw sztucznych którymi dodatkowo powleka się gumę.
W przypadku węży konstrukcyjnie sztywnych (np. na skutek zastosowania wykładziny ze tworzywa) zwiększa się ich elastyczność stosując fałdowanie (karbowanie) warstwy zewnętrznej.
W wielu zastosowaniach warstwa zewnętrzna pełni też funkcję identyfikacyjną: posiada określony kolor lub trwałe oznakowanie przyjęte dla danego rodzaju aplikacji.
Końcówki
W większości zastosowań węży technicznych mamy na myśli zastosowanie związane z nadciśnieniem lub podciśnieniem – stąd odpowiednie wzmocnienia węży. W tym celu – aby móc podłączyć wąż do instalacji – konieczne jest odpowiednie zamocowanie do węża końcówek. Musimy zawsze pamiętać, że końcówki i ich mocowanie muszą spełniać wszystkie oczekiwane parametry pracy, tzn. zakres ciśnień, temperatur i posiadać odpowiednią odporność chemiczną.
Kwestia przyłączy jest odrębnym zagadnieniem i zasadniczo sprowadza się prawidłowego określenia potrzebnego standardu, rodzaju, wielkości i materiału potrzebnego złącza. W tym miejscu chcielibyśmy skupić się wyłącznie na kwestii połączenia końcówki w wężem.
Węże gumowe oferują kilka dostępnych rozwiązań w zakresie sposobu mocowania końcówek. Można je ogólnie podzielić na cztery kategorie:
Mocowanie za pomocą opasek…
lub nie podtrzymujących końcówki obejm są najprostszym, tradycyjnych sposobem samodzielnego montażu końcówek. Stosuje się je do mocowania końcówek karbowanych, wciskanych do węża gumowego lub z tworzyw termoplastycznych. Ważne jest aby opaska/obejma umożliwiała odpowiednio mocne ściśnięcie węża, tak aby końcówka nie wysunęła się pod wpływem zmian ciśnienia w wężu. Dla zwiększenia bezpieczeństwa należy stosować po dwie opaski dla każdej z końcówek.
Mocowanie za pomocą obejm lub tulei skręcanych…
jest odpowiedzią na potrzebę poprawy jakości mocowania końcówek, pewności wykonania poprawnego montażu przy zachowaniu możliwości demontażu i osiągnięcia wyższych parametrów bezpiecznej pracy. W przypadku systemów ze skorupami końcówki o odpowiednio ukształtowanym ogonie tworzą wraz ze skorupami jeden system. Mocna, odporna na odkształcenia obejma odpowiednio dobrana do średnicy nominalnej i grubości ścianki węża ściska go centrycznie mocno i równomiernie do gładkiej końcówki przy pomocy śrub. Jednocześnie skorupa bezpośrednio przytrzymuje zazębieniem metalową końcówkę. Pod względem wytrzymałości daje to efekt zbliżony do zaciśnięcia tulei metalowej przy pomocy prasy. Tego typu końcówki stosuje się obecnie powszechnie do węży gumowych do przesyłu paliw oraz do substancji chemicznych. Podobne rozwiązanie zostało także opracowane i przyjęte dla węży do pary wodnej.
Mocowanie za pomocą zaprasowania…
jest rozwiązaniem powszechnie stosowanym w przewodach hydrauliki siłowej – ze względu na wytrzymałość – ale też często stosowanym w wymagających zastosowaniach węży technicznych. Zaprasowanie metalową tuleją zapewnia wytrzymałość mechaniczną, ale też gwarantuje brak możliwości nieuprawnionego demontażu. Tuleja ma mniejsze gabaryty zewnętrzne i jest łatwiejsza do utrzymania w czystości niż opaski czy skorupy. Ponadto, dzięki tej technologii można uzyskać optymalny i równomierny docisk warstwy wewnętrznej węża do końcówki zapobiegając powstawaniu martwych przestrzeni i zastoin medium. W specjalnych sytuacjach stosuje się prasowanie końcówki od wnętrza, dzięki czemu końcówka zachowuje dokładnie średnicę otworu taką jak wąż. Ułatwia to przesył substancji o dużej gęstości i zawiesin, a także zapewnia możliwość dokładnego oczyszczenia węża np. przy pomocy pigowania.
Integralnie wulkanizowane lub mankiety
Istnieje kilka przypadków w których najlepszym rozwiązaniem jest zabudowanie końcówki bezpośrednio w trakcie budowy węża gumowego. Oczywiście długość takiego przewodu pozostanie niezmienna, natomiast uzyskamy pełne, integralne związanie końcówki ze wzmocnieniem węża. Tego typu wykonanie daje jeszcze inną, unikalną możliwość: warstwę wewnętrzną węża można bezpośrednio, poprzez końcówkę, wyprowadzić aż na powierzchnię uszczelniającą. Jest to szczególnie cenne dla zastosowań chemicznych, gdzie metalowa końcówka jest w ten sposób chroniona przed bezpośrednim działaniem medium. Wulkanizowanie integralne stosuje się też często dla przewodów o dużych i bardzo dużych średnicach (powyżej DN150mm). (Patrz: kilka przykładowych rozwiązań mocowania integralnego). Dla niektórych specjalistycznych przewodów z kolei istnieje potrzeba wykonania miękkiego zakończenia (mankietu) który umożliwi łatwe umocowania przy pomocy zwykłej opaski zaciskowej.
Przykładowe zastosowania przewodów gumowych
Przewody przeładunkowe do autocystern i cystern kolejowych (paliwa samochodowe i lotnicze, LPG, substancje chemiczne) oraz do przeładunków morskich.
Przewody do zwijaczy dla autocystern cystern kolejowych (paliwa samochodowe i lotnicze, LPG, substancje chemiczne).
Przewody dla stanowisk załadunku i rozładunku (UNO).
Przewody dla instalacji technologicznych w zakładach chemicznych i petrochemicznych.
Przewody do transportu pneumatycznego substancji ściernych i piaskowania.
Przewody do przesyłu mokrych substancji ściernych.
Przewody do autocystern dla produktów spożywczych (mleko, soki, woda pitna, napoje zawierające alkohol, płynna czekolada, oleje roślinne).
Przewody dla instalacji technologicznych w zakładach produkcji spożywczej.
PRZEWODY KOMPOZYTOWE
Rozwój w produkcji tworzyw sztucznych o doskonałych własnościach fizycznych i odporności chemicznej dał impuls do powstania węży wielowarstwowych, całkowicie pozbawionych gumy i litego, grubego tworzywa. Wiele odpowiednio dobranych warstw składających się ze szczelnej folii oraz tkanin z tworzyw sztucznych ściśniętych pomiędzy spiralami z drutu metalowego tworzy wąż, podczas gdy wyprofilowane ogony końcówek, uszczelki i zaprasowana metalowa tuleja zapewniają szczelne i trwałe osadzenie końcówek. Ze względu na konstrukcję, węże kompozytowe charakteryzuje wysoka i praktycznie niezależna od temperatury elastyczność dla której chętnie stosowane są na autocysternach. Bogactwo dostępnych materiałów konstrukcyjnych pozwala wykonać w tej technologii węże dla ekstremalnie niskich (płynne gazy) i wysokich (substancje bitumiczne) temperatur, zintegrować w strukturze węża najnowocześniejsze materiały termoizolacyjne (cryogel) czy odporne na ogień lub substancje chemiczne, tak aby finalnie wąż dokładnie odpowiadał wymagającym zastosowaniom. Bardzo istotną zaletą węży kompozytowych jest możliwość wykonania ich w bardzo dużych średnicach (do DN 300) i w dość długich odcinkach (do 25 m). Są one wobec tego dobrą alternatywą do węży gumowych w przeładunkach masowych, np. statek-nabrzeże.
Warstwa wewnętrzna
zależnie od przeznaczenia węża dobierana jest warstwa wewnętrzna. Zazwyczaj jest to PP, PE lub PTFE zapewniające właściwą odporność chemiczną. Ponieważ wewnętrzna spirala również jest wystawiona na bezpośrednie działanie medium, jej materiał również musi być odpowiedni. Do wyboru mamy aluminium, stal ocynkowaną stale nierdzewne i kwasoodporne a nawet tytan. Dodatkowo, możemy zastosować drut powlekany tworzywem sztucznym: PP lub PVDF. Zaletą odkrytych, metalowych spiral jest zapewnienie dobrych możliwości odprowadzania ładunków statycznych z wnętrza węża do metalowych końcówek w aplikacjach które tego wymagają.
Widoczną wadą węży kompozytowych jest brak gładkości warstwy wewnętrznej i utrudnionego w związku z tym oczyszczania z medium. Z tego samego powodu tłumienie przepływu jest większe niż w przypadku klasycznego węża gumowego.
Wzmocnienie
podczas gdy spirala wewnętrzna zapewnia dobrą odporność na podciśnienie, za wytrzymałość na nadciśnienie odpowiadają spiralnie nawinięte warstwy tkanin. Węże kompozytowe na rynek europejski (EN 13765: 2010) najczęściej wykonuje się w dwóch klasach ciśnieniowych: 10 bar i 15 bar.
W niektórych wersjach w warstwie wzmacniającej stosuje się pewne dodatkowe warstwy, np. zapobiegające migracji przewodzonego medium czy stanowiące barierę ochronną, np. termiczną.
Warstwa zewnętrzna
jak zawsze pełni funkcję ochronną. Najczęściej jest to tkanina pokryta winylem ułatwiająca utrzymanie węża w czystości. Ze względu na dostępność jaskrawych kolorów klienci często zamawiają własne opcje służące łatwej identyfikacji wizualnej poszczególnych przewodów przeznaczonych do różnych cieczy. W zastosowaniach specjalny, które tego wymagają (ATEX) stosowane są tkaniny posiadające własności antyelektrostatyczne.
Oczywiście, nie do pominięcia jest zewnętrzny drut wzmacniający. W zależności od potrzeb może on być aluminiowy (waga), stalowy ocynkowany (ekonomia), nierdzewny lub kwasoodporny (środowiska korozyjne) lub stalowy powlekany tworzywem (również dla zabezpieczenia przed korozją).
Końcówki
muszą być zawsze dedykowane dla węży kompozytowych określonego producenta (skok i kierunek skrętu spirali) a ich montaż należy pozostawić wyłącznie wykwalifikowanemu personelowi. Niezbędne są odpowiednie prasy do zaciskania tulei oraz doświadczenie.
Przykładowe zastosowania przewodów kompozytowych
Przewody przeładunkowe do autocystern i cystern kolejowych (paliwa samochodowe i lotnicze, substancje chemiczne) oraz do przeładunków morskich
Przewody dla stanowisk załadunku i rozładunku (UNO)
Przewody dla instalacji technologicznych w zakładach chemicznych i petrochemicznych
PRZEWODY METALOWE
Elastyczne węże metalowe wykonane z fałdowanej cienkościennej blachy metalowej i wzmocnione oplotem z drutu zajmują znaczące miejsce wśród dostępnych rozwiązań przewodów elastycznych. Są całkowicie gazoszczelne, mogą być stosowane dla najszerszego zakresu temperatur roboczych, są całkowicie niepalne i mają naturalną zdolność odprowadzania ładunków statycznych. Ponieważ są dostępne w bardzo dużym zakresie średnic, wersjach wykonań zapewniających różny stopień elastyczności i wytrzymałości ciśnieniowej można je odnaleźć w wielu, bardzo różnych obszarach zastosowań.
Ponieważ montaż końcówek wymaga wykonania specjalistycznego spawu tego rodzaju węże dostarczane są użytkownikom wyłącznie w postaci gotowych przewodów z końcówkami poddanych uprzednio próbie szczelności.
Warstwa wewnętrzna
wykonana jest z cienkiej, fałdowanej blachy ze stali nierdzewnej. Stosuje się kilka gatunków stali nierdzewnej bądź stopy specjalne takie jak Monel ® czy Hastelloy® – ze względu na potrzebę podwyższonej odporności na korozję. Stosuje się różne profile i metody fałdowania dające w efekcie zróżnicowaną elastyczność węża oraz wytrzymałość i trwałość. Fałdowanie zapewnia również wężom metalowym wysoką odporność na podciśnienie.
Wzmocnienie
na nadciśnienie zapewnia zasadniczo zewnętrzny oplot z drutu. W celu odpowiedniego zwiększenia wytrzymałości stosuje się dwa lub trzy oploty oraz specjalne rodzaje splotu drutu wykonanego z jednego z gatunków stali nierdzewnych.
Końcówki
muszą być przyspawane w taki sposób aby uzyskać pełną szczelność fałdowanej warstwy wewnętrznej z cienkiej blachy oraz połączyć wszystkie końce drutów tworzących oplot. Dodatkowo, dla wymagających zastosowań chemicznych i spożywczych spaw powinien być wykonany w taki sposób aby wewnątrz końcówki, po spawaniu, nie pozostały wystające ostre krawędzie spawanego płaszcza wewnętrznego. Materiał końcówki powinien wewnątrz płynnie przechodzić w blachę płaszcza. Wykonanie tego rodzaju spawu wymaga szczególnych kwalifikacji ze strony spawacza.
Przykładowe zastosowania przewodów metalowych
Przewody przeładunkowe do autocystern i cystern kolejowych ( substancje chemiczne i gazy techniczne) oraz do przeładunków morskich
Przewody dla stanowisk załadunku i rozładunku (UNO)
Przewody dla instalacji technologicznych w zakładach chemicznych i petrochemicznych.
Przewody podgrzewane.
Minimalna długość przewodu metalowego
Aby wąż metalowy mógł spełnić wymagania dotyczące charakterystyki określone w normie, długość efektywna węża (część elastyczna pomiędzy końcówkami) musi być taka, aby splotka oplotu wykonała co najmniej 1 pełny obrót.
Nominalna średnica wewnętrzna [mm] | 6 | 8 | 10 | 12 | 15 | 20 | 25 | 32 | 40 | 50 | 65 | 80 | 100 | 125 | 150 | 200 | 250 |
Minimalna długość std. węża metalowego z oplotem [mm] | 40 | 45 | 55 | 65 | 80 | 95 | 115 | 135 | 165 | 210 | 260 | 345 | 400 | 460 | 550 | 720 | 900 |
Biorąc pod uwagę niezbędną długość końcówek, najkrótszy, konstrukcyjnie dopuszczalny przewód, może się okazać zbyt długi, biorąc pod uwagę dostępne miejsce do zabudowy. W takiej sytuacji konieczną elastyczność może zapewnić zastosowanie kompensatora zamiast węża.
PRZEWODY SILIKONOWE
Węże silikonowe które są stosowane do wykonywania przewodów gotowych w zasadzie konstrukcyjnie są takie jak węże gumowe. Różnica polega zasadniczo na zastosowaniu czystej, przezroczystej gumy silikonowej która przeważnie jest również bardziej miękka niż rodzaje gumy stosowane w wężach technicznych. Ponieważ tego typu węże przeznaczone są do stosowania w aplikacjach wymagających wysokiej czystości i często sterylizacji jeszcze większe znaczenie ma odpowiednie wykonanie mocowania końcówki. Musi ono być tak wykonane aby nie powstawały martwe przestrzenie i uskoki uniemożliwiające dokładne oczyszczenie węża, ale też w taki sposób aby nie uszkodzić stosunkowo delikatnego materiału węża. Gotowe węże silikonowe w trakcie eksploatacji często poddawane są w całości okresowej sterylizacji np. w autoklawie.
Ponieważ montaż końcówek zaciskanych wymaga dużej praktyki ze strony operatora tego typu węże dostarczamy głównie w postaci gotowych przewodów z końcówkami.
Warstwa wewnętrzna
wykonana jest z przezroczystej gumy silikonowej.
Wzmocnienie
węża stosownie do przewidzianego rodzaju pracy: tłocznej lub ssawno-tłocznej uzyskuje się je odpowiednio kordem tekstylnym lub oplotami z włókien dla uzyskania wytrzymałości ciśnieniowej oraz spiralą ze stali – dla uzyskania wytrzymałości na podciśnienie.
Warstwa zewnętrzna
ma za zadanie chronić wąż i zapewnić gładkość umożliwiającą dokładne oczyszczenie. W przypadku węży silikonowych najczęściej warstwa wewnętrzna wykonywana jest z takiego samego gatunku silikonu jak warstwa wewnętrzna. Niekiedy zamiast gumy przeźroczystej stosuje się gumę białą. Dla zachowania najwyższej czystości stosuje się proces sieciowania platyną.
Końcówki
oraz tuleje zaciskowe muszą być odpowiednio dostosowane do większej miękkości gumy silikonowej i zapewniać optymalny zacisk bez nadwyrężenia materiału. Końcówki wyposażone są w złącza charakterystyczne dla instalacji wymagających zachowania najwyższej czystości. Szczególnie popularne są róże standardy złączy łączonych klamrą typu Triclamp jak również specjalizowane połączenia gwintowe DIN 11851 oraz SMS 1145.
Przykładowe zastosowania węży silikonowych
Przewody do przesyłu cieczy w produkcji farmaceutycznej.
Przewody do przesyłu cieczy w produkcji kosmetycznej.
Przewody do przesyłu cieczy w produkcji spożywczej.
PRZEWODY TEFLONOWE
Klasyczne węże teflonowe składają się z odpowiednio grubej warstwy wewnętrznej PTFE i zewnętrznego wzmocnienia oplotem, najczęściej wykonanym z drutu ze stali nierdzewnej. Dzięki wyjątkowym własnościom PTFE węże o tej konstrukcji stosowane są chętnie w bardzo różnych obszarach przemysłu. Materiał ten doskonale nadaje się do zastosowań wymagających wysokiej czystości, posiada znakomitą odporność na większość substancji chemicznych i nie zawiera żadnych toksycznych dodatków. Może także być stosowany w bardzo szerokim zakresie temperatur – istotnie szerszym niż dostępny dla węży gumowych. Nie ulega procesowi starzenia jak guma.
Dodatkowo wewnętrzną warstwę PTFE można wyprowadzić poprzez końcówkę na zewnątrz i trwale uformować na powierzchni uszczelniającej złącza, dzięki czemu metal końcówki może być całkowicie chroniony przed oddziaływaniem przepływającego medium.
Węże z PTFE są bardzo uniwersalne ale trzeba pamiętać o kilku charakterystycznych ograniczeniach dla tego typu konstrukcji:
– wraz ze wzrostem temperatury mocno spada wytrzymałość tuby teflonowej (tworzywo mięknie),
– standardowe PTFE posiada istotny poziom przenikalności dla niektórych gazów. Istnieją specjalne wykonania w których PTFE jest poddawane dodatkowej obróbce zmniejszającej normalny poziom przenikalności dla cząsteczek gazów.
– warstwa teflonu jest delikatna i stosunkowo łatwo uszkodzić ją mechanicznie, np. podczas oczyszczania lub przy montażu.
Montaż końcówek do węży z PTFE wymaga użycia specjalistycznych urządzeń i narzędzi oraz dostosowanych, specjalnych końcówek. Konieczne jest co najmniej użycie prasy, a w przypadku końcówek integralnie powlekanych – obróbki termicznej. Z tych powodów przewody z PTFE dostarczamy użytkownikom wyłącznie w formie gotowej – z zamontowanymi końcówkami.
Warstwa wewnętrzna
Ponieważ PTFE jest tworzywem stosunkowo sztywnym, dla zapewniania odpowiedniej elastyczności, zwłaszcza dla większych średnic węży stosuje się fałdowanie lub zewnętrzne karbowanie tuby teflonowej. Fałdowanie najczęściej jest spiralne, dzięki czemu unika się powstawania zastoin w fałdach węża – przepływająca ciecz może wypłukać ewentualne osady. Grubość tuby PTFE wynosi od niecałego 1 mm dla węży o najmniejszych średnicach nominalnych (DN 5 mm) do kilku milimetrów w przypadku średnic większych (maksymalnie DN 150 mm). Stosowane są dwie wersje PTFE – naturalne, przejrzyste oraz czarne – antystatyczne. Tuby gładkościenne stosuje się typowo w rozmiarach do DN 25mm – powyżej tej granicy, bez dodatkowych zabiegów stają się zbyt sztywne i podatne na załamanie. Natomiast tuby fałdowane stosuje się aż do największych średnic – zapewniają one bardzo wysoką elastyczność węża i uzyskanie małego minimalnego promienia zagięcia.
Wzmocnienie
węża dla pracy ciśnieniowej uzyskuje się dzięki zewnętrznemu oplotowi wzmacniającemu, podobnie jak w przypadku węży metalowych. Najczęściej wykonany jest on z drutu ze stali nierdzewnej, ale spotyka się też oploty z tworzyw sztucznych: PP i PVDF. Dość dużą wytrzymałość na podciśnienie zapewnia sztywność samego tworzywa oraz fałdowany profil. Natomiast w zastosowania wymagających jeszcze większej wytrzymałości stosuje się dodatkową spiralę z drutu nawiniętą spiralnie wokół węża.
W zaawansowanych wersjach stosuje się dodatkowe powleczenia np. przy pomocy wulkanizowanej gumy która zapewnia dodatkową ochronę węża czy łatwiejsze utrzymanie go w czystości lub elementy wzmacniające wąż w pobliżu samej końcówki (zabezpieczenie przed załamaniem) i podobne akcesoria.
Końcówki
oraz tuleje zaciskowe muszą być odpowiednio dostosowane do właściwości stosunkowo cienkiej tuby, tak aby zbyt ostre krawędzie lub zbyt głębokie przetłoczenia podczas zaciskania nie spowodowały jej uszkodzenia. Znacznie trudniejsze jest wykonanie integralnego powleczenia końcówki, tzn. wyprowadzenia tuby teflonowej z węża poprzez otwór końcówki na zewnątrz a następnie takie uformowanie PTFE na gorąco aby tworzywo pokrywało całą powierzchnię uszczelniającą złącza. Zyskujemy dzięki temu brak jakichkolwiek zagłębień naturalnie występujących w przypadku zaciskania teflonu na wsuniętej do węża końcówce – czyli możliwość dokładnego oczyszczania węża oraz ochronę przed kontaktem metalu końcówki z medium roboczym – co ma podstawowe znacznie dla mediów ultra czystych lub bardzo agresywnych dla metali.
Przykładowe zastosowania węży teflonowych
Przewody do przesyłu cieczy w produkcji farmaceutycznej, kosmetycznej lub spożywczej.
Przewody do procesów technologicznych w chemii i petrochemiach.
Przewody uniwersalne do przeładunków substancji chemicznych.
Przewody do pary (przemysł gumowy: formy do wulkanizacji, ogrzewanie i podgrzewanie instalacji, para technologiczna).
Przewody podgrzewane do klejów (np. PU).
PRZEWODY Z TWORZYW SZTUCZNYCH
Coraz częściej węże wykonywane całkowicie z nowoczesnych tworzyw termoplastycznych zastępują w popularnych zastosowaniach węże gumowe. Niektóre z nich w praktyce konstrukcją i wyglądem są dokładnymi odpowiednikami węży gumowych i są wyposażane w końcówki w taki sam sposób jak węże gumowe (za wyjątkiem wulkanizacji). Pozostałe posiadają odmienne konstrukcje. Taką bardzo popularną grupą są węże z ekstrudowanego tworzywa elastycznego (najczęściej różne odmiany PCV i PU) wzmacniane spiralą z twardego tworzywa (najczęściej PCV, rzadziej spirala z drutu metalowego lub inne rodzaje tworzyw sztucznych). Tego rodzaju węże posiadają z reguły bardzo dobrą wytrzymałość na podciśnienie i pewną wytrzymałość na nadciśnienie – mocno zależną od rodzaju materiału i jego grubości. Istnieją oczywiście wersje dodatkowo wzmacniane oplotem dla pracy nadciśnieniowej. Zalet tego rodzaju węży jest kilka:
– są lżejsze niż węże gumowe
– dostępne są wersje przejrzyste umożliwiające obserwację wnętrza przewodu poprzez jego ściankę
– generalnie są tańsze i łatwiej dostępne w różnych wersjach niż węże gumowe
– często mogą wykazać się lepszą odpornością i trwałością niż węże gumowe w analogicznych aplikacjach
Ograniczeniem dla tego typu węży są najczęściej ograniczona wytrzymałość mechaniczna i stosunkowo wąski zakres temperatur pracy.
Montaż końcówek jest najczęściej realizowany samodzielnie przez użytkowników, przy pomocy standardowo dostępnych na rynku opasek mocujących. Coraz częściej jednak użytkownicy zainteresowani są nabywaniem przewodów gotowych do użytku z zamontowanymi końcówkami. Ponieważ uniwersalne opaski mocujące są niezbyt ergonomiczne w codziennym użytkowaniu (mocno wystające poza obrys węża elementy, ostre krawędzie) popularne staje się mocowanie końcówek tulejami zaciskanymi.
polecamy produkty firmy IPL
Wzmocnienie
stanowi spirala z twardego tworzywa (np. PCV) lub drutu. Dodatkowo dla pracy tłocznej stosuje się wzmocnienie oplotem. Często, dla zapewnienia własności antystatycznych równolegle do spirali wzmacniającej z tworzywa wprowadza się miedzianą linkę. Oprócz tego tradycyjnego rozwiązania w ostatnich latach pojawia się coraz więcej tworzyw sztucznych zapewniających trwałe własności antyelektrostatyczne (rezystancje w zakresie od 104 do 108 Ω).
Zaawansowane węże wykonywane są w różnych kombinacji tworzyw łączonych w procesie produkcji i tak coraz więcej stosowanych jest wiele odmian poliuretanów – jako tworzywo konstrukcyjne lub jako wykładzina. Uzyskuje się dzięki temu ogromny wzrost odporności na ścieranie wnętrza węża, wzrost jego elastyczności czy poszerzenie dostępnego zakresu temperatur roboczych.
Przykładowe zastosowania przewodów z tworzyw sztucznych
Przewody do pomp i ścieków
Zestawy grawitacyjne
Przewody dla przemysłu spożywczego
Końcówki
stosowane są najczęściej uniwersalne , karbowane, podobne jak dla węży gumowych. Biorąc jednak pod uwagę mniejszą podatność tradycyjnych tworzyw termoplastycznych na rozciąganie niż gumy wkładanie końcówek do węży, zwłaszcza o większych średnicach bywa trudniejsze. Do mocowania końcówek stosuje się najczęściej opaski. Dla bezpieczeństwa zaleca się stosowanie dwóch opasek na każdą końcówkę.
Można także mocować końcówki przy pomocy zaprasowywanych tulei.
PRZEWODY PŁASKO ZWIJALNE
Nowoczesne węże płasko zwijalne są niezastąpione w sytuacjach kryzysowych, ponieważ są łatwe w transporcie ze względu na minimalne gabaryty po zwinięciu i mniejszy ciężar od tradycyjnych węży. Są też dostępne w bardzo długich odcinkach – 100 a nawet 200 m, dzięki czemu możliwe jest szybkie ułożenie tymczasowego elastycznego rurociągu na duże odległości. Jednakże w wielu dziedzinach, takich jak rolnictwo, budownictwo i górnictwo ze względu na swoje liczne zalety stały się standardowym, choć wysoko wyspecjalizowanym, narzędziem pracy dla profesjonalistów.
Budowa węża
Płaszcz węża zapewniający odpowiednią wytrzymałość na rozerwanie i stabilność pod ciśnieniem wykonywany jest metodą wyplatania ze specjalnie dobranych włókien, najczęściej poliamidowych i poliestrowych. Następnie, w specjalnym procesie poprzez ten splot wytłaczana jest pod wysokim ciśnieniem odpowiednio dobrana mieszanka gumy lub tworzywa sztucznego. Jeśli stosowana jest mieszanka gumowa, to wąż poddawany jest procesowi wulkanizacji. Dzięki temu splot z tkaniny jest całkowicie zatopiony w gumie lub tworzywie i dzięki temu chroniony zarówno przed kontaktem z medium przepływającym przez wąż jak i czynnikami zewnętrznymi. Tak wykonana ścianka węża jest mocna i cienka, dzięki czemu rolka zwiniętego przewodu ma niewielkie gabaryty i jest znacznie lżejsza niż tradycyjnych przemysłowych węży gumowych. Niezaprzeczalną zaletą tej technologii jest możliwość wyprodukowania bardzo długich odcinków węży, również o dużych średnicach – do DN 356 mm, mogących pracować pod ciśnieniem roboczym do 10 barów! Standardowo, dostępne są odcinki długości 100 a nawet 200 m.
Najczęściej stosowana jest mieszanka gumy nitrylowej oraz poliuretany. W zależności od zastosowania mogą to być poliuretany polieterowe (odporne na hydrolizę i czynnki biologiczne), spełniającego wymagania dla wody pitnej bądź poliestrowe (odporne na paliwa i produkty ropopochodne)
W przypadku gdy węże są przeznaczone do substancji, które wymagają zapewnienia możliwości odprowadzania ładunków elektrostatycznych do warstwy wzmocnienia wprowadzane są miedziane przewody antystatyczne, które łączy się z metalowymi końcówkami.
Węże ze płaskie gumowane są często optymalnym rozwiązaniem, łączącym uniwersalność i elastyczność z przystępną ceną. Węże poliuretanowe są niezastąpione w zastosowaniach gdzie wymagana jest ekstremalna wytrzymałość lub występują skrajnie niskie temperatury: do -50°C.
Mocowanie końcówek
Popularnym, podstawowym fabrycznym sposobem mocowania końcówek jest tzw. taśmowanie, czyli zaciskanie węża przy pomocy nawijania odpowiednio naprężonego drutu. Metoda ta wymaga stosowania wyspecjalizowanych narzędzi montażowych.
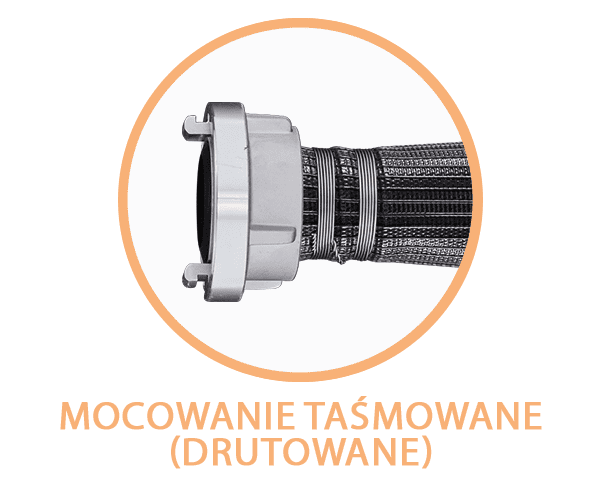
W przypadku samodzielnego montażu końcówek stosowane są odpowiednio dobrane opaski metalowe ściągane śrubą.

Dla węży wymagających zwiększonej wytrzymałości stosuje się końcówki specjalne współpracujące z dedykowanymi obejmami segmentowymi ściąganymi śrubami.
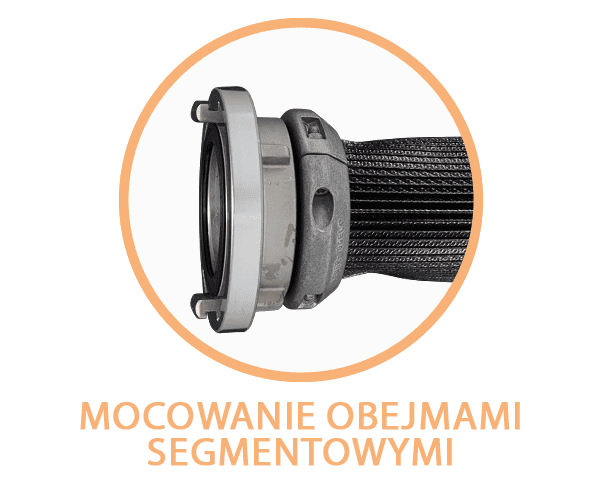
Do węży dużych średnicach wymagających szczególnie wytrzymałego mocowania stosuje się specjalne końcówki U.S. Shug.
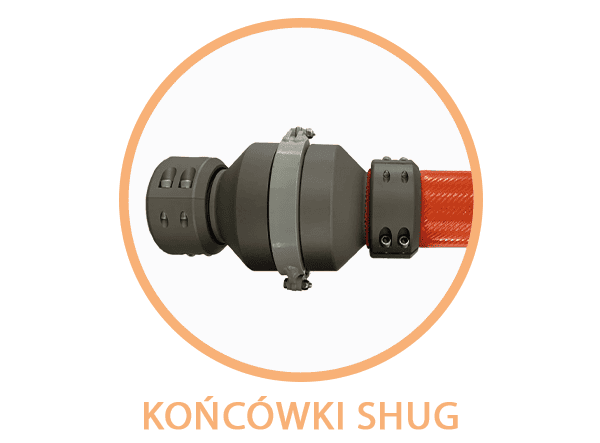
Przykładowe zastosowania przewodów płasko zwijalnych
Wojsko i sytuacje kryzysowe: woda i paliwa

Budownictwo i górnictwa: woda, sprężone powietrze, beton i zaprawy, woda pitna

Woda pitna: wydobycie i przesył

Rolnictwo: nawadnianie i nawożenie

Specjalne: naśnieżanie, osłona i inne
